1. Supplier Reliability and Communication
Reliable Suppliers: Partnering with reliable suppliers is foundational. Evaluate potential suppliers based on their track record for punctuality, quality, and responsiveness.
Effective Communication: Maintain open and consistent communication with suppliers. Regular updates on production schedules, potential delays, and logistics are vital for proactive planning.
2. Inventory Management
Buffer Stock: Maintain an adequate buffer stock to cushion against unforeseen delays. This practice helps mitigate risks associated with supply chain disruptions.
Demand Forecasting: Utilize advanced forecasting techniques to predict demand accurately. This ensures that inventory levels are aligned with market needs, preventing both stockouts and overstock situations.
3. Logistics and Transportation
Efficient Logistics Partners: Choose logistics partners with a proven track record for timely delivery. Their efficiency directly impacts the supply chain’s ability to meet delivery deadlines.
Optimized Shipping Routes: Analyze and select the most efficient shipping routes. Consider factors such as transit time, customs clearance procedures, and potential geopolitical issues.
4. Technology Integration
Supply Chain Management Software: Implement robust supply chain management software to streamline operations. Such systems enhance visibility, track shipments in real-time, and facilitate better decision-making.
Automation: Embrace automation to reduce manual errors and accelerate processes. Automated systems can handle tasks such as order processing, inventory updates, and shipment tracking with greater accuracy and speed.
5. Quality Control
Regular Audits: Conduct regular audits of suppliers to ensure adherence to quality standards and timelines. This practice helps identify and rectify potential issues before they escalate.
Third-Party Inspections: Employ third-party inspection services to verify the quality and compliance of products before shipment. This step ensures that only defect-free products are delivered, reducing delays caused by returns or rework.
6. Risk Management
Diversified Supplier Base: Avoid reliance on a single supplier. Diversifying the supplier base reduces the risk of disruptions and provides alternative options in case of delays.
Contingency Planning: Develop comprehensive contingency plans for various scenarios, such as natural disasters, political instability, or supplier insolvency. Having a clear action plan helps maintain operations during unforeseen events.
7. Compliance and Documentation
Regulatory Compliance: Stay updated on international trade regulations and ensure compliance. Non-compliance can lead to delays at customs and border crossings.
Accurate Documentation: Ensure that all shipping documents are accurate and complete. Inaccurate documentation can cause significant delays in customs clearance and delivery.
8. Collaboration and Partnerships
Strategic Partnerships: Build strategic partnerships with key players in the supply chain, such as manufacturers, logistics providers, and distributors. Collaborative relationships foster trust and efficiency.
Continuous Improvement: Engage in continuous improvement initiatives with partners. Regularly review and refine processes to enhance overall supply chain performance.
By focusing on these key factors, B2B buyers can effectively manage their global supply chains and ensure the timely delivery of melamine dinnerwares. Adopting a proactive approach to supply chain management not only mitigates risks but also enhances operational efficiency and customer satisfaction.
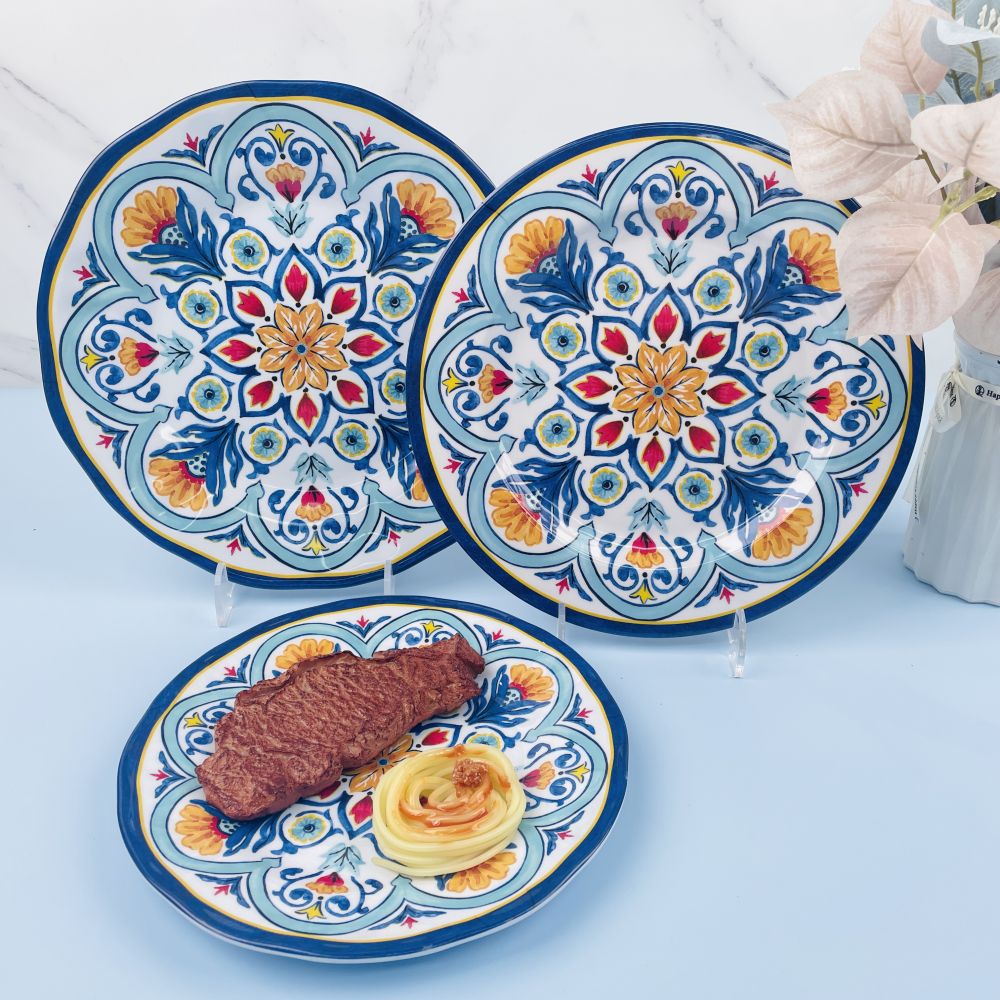
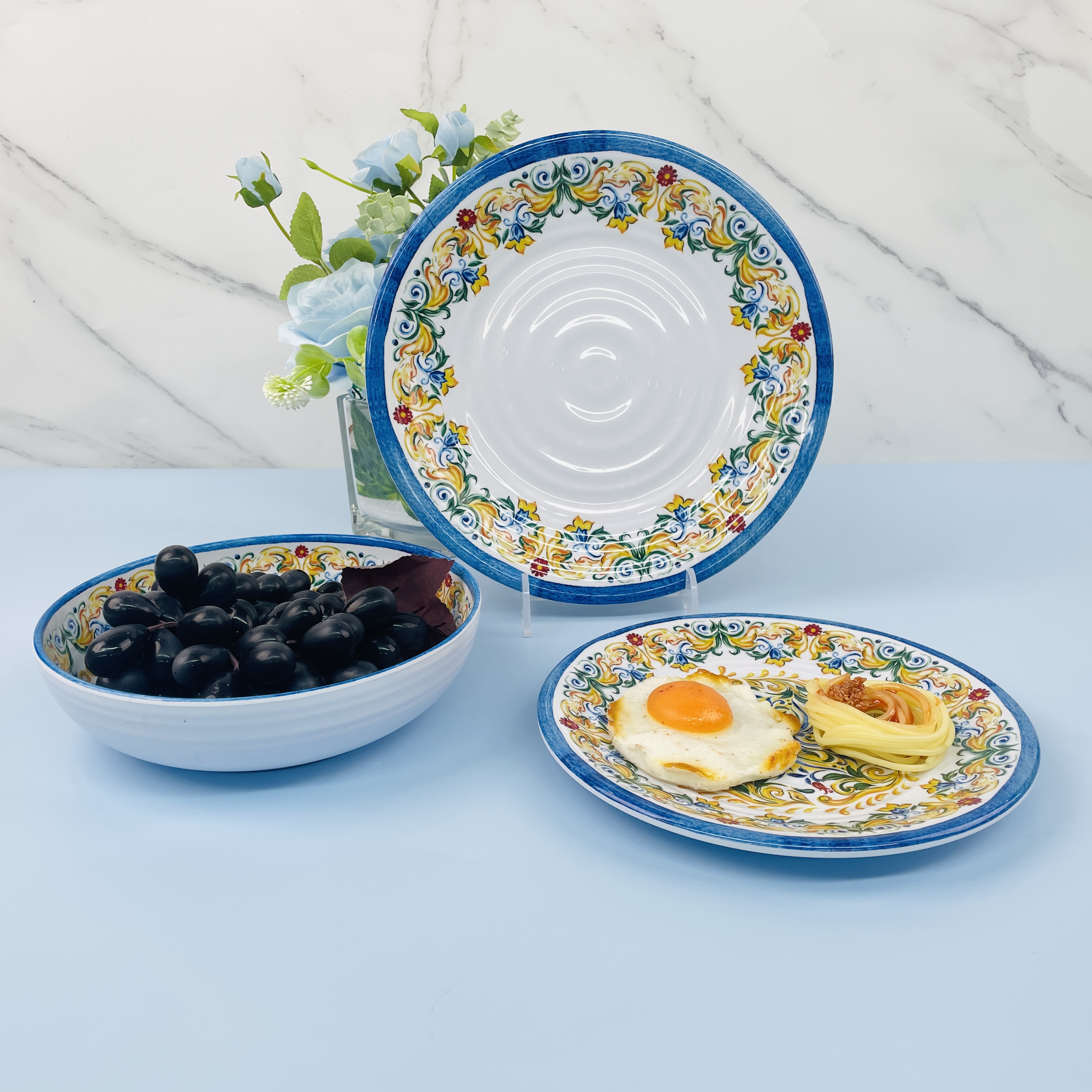
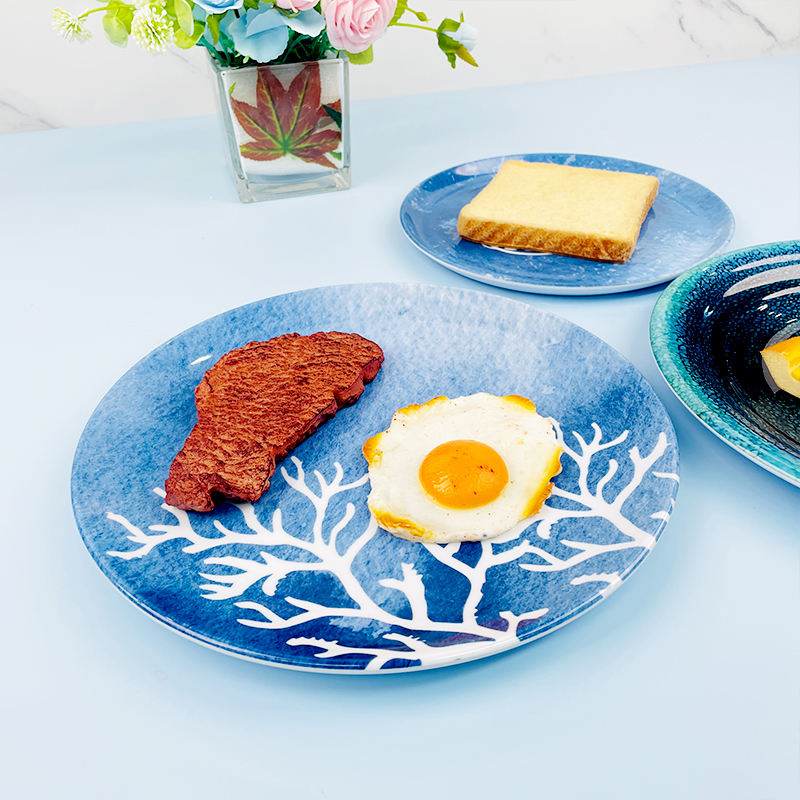
About Us

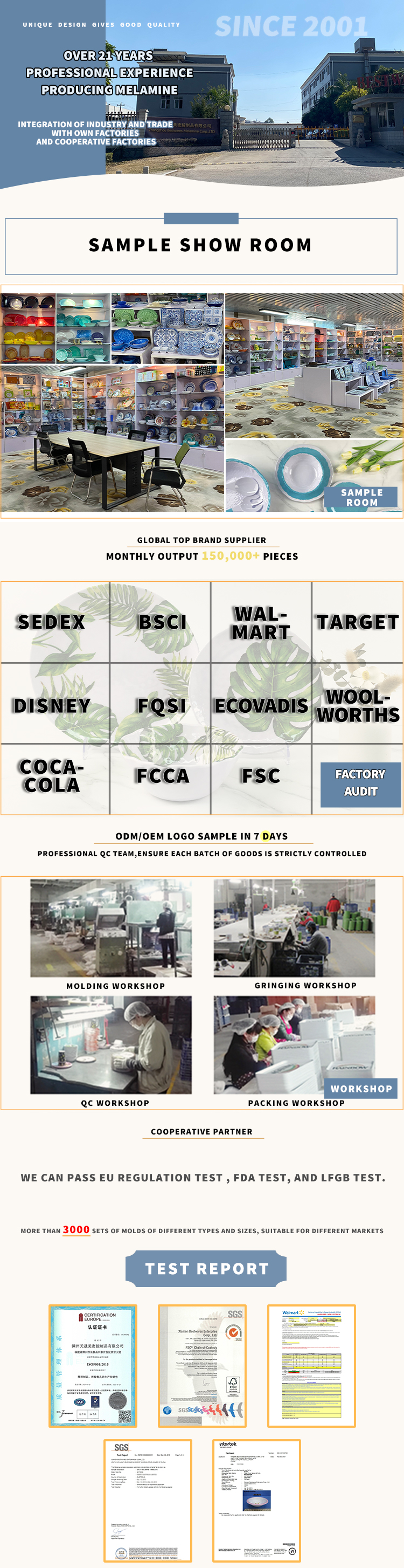
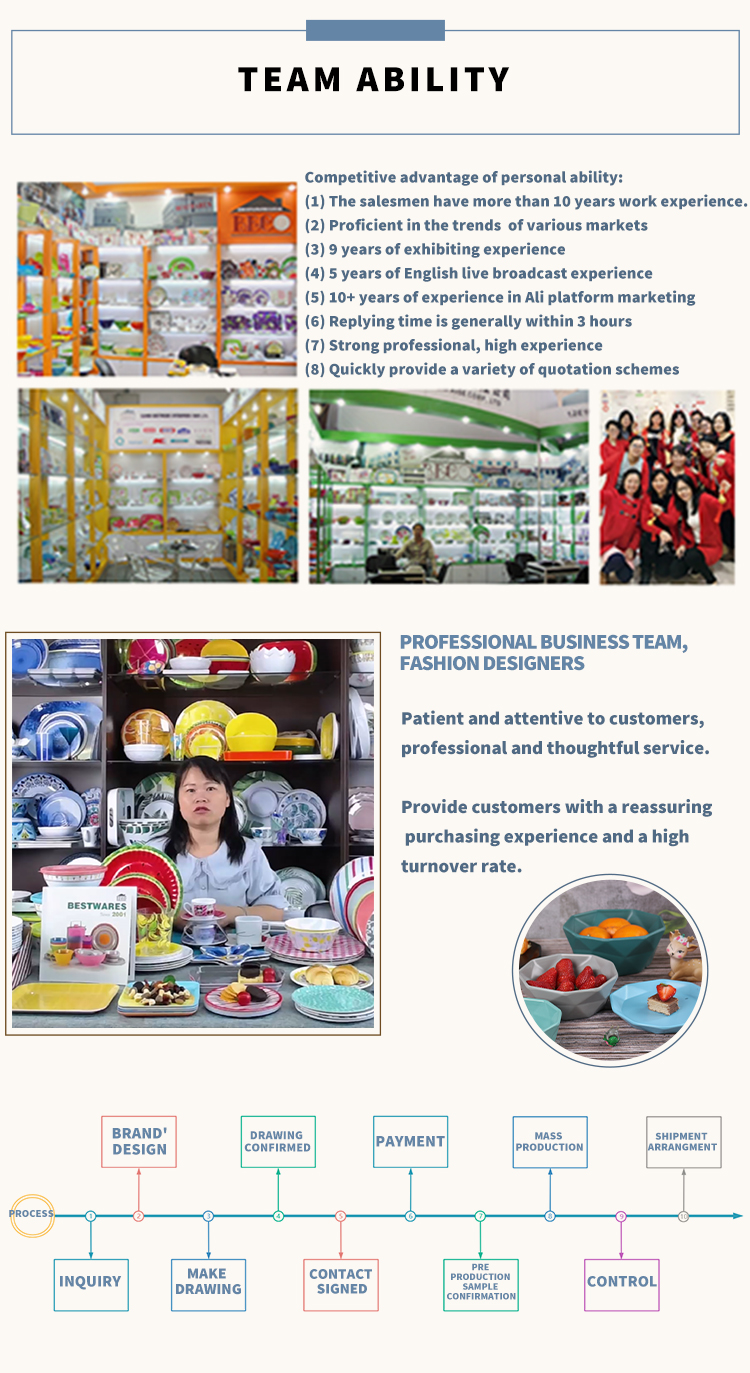
Post time: Aug-02-2024