1. Raw Material Selection
High-Quality Melamine Resin: The manufacturing process begins with the selection of high-quality melamine resin, which serves as the foundation for the entire product. The purity of the resin affects the strength, safety, and appearance of the final dinnerware. Manufacturers must source premium raw materials from reliable suppliers to ensure consistent product quality.
Additives and Colorants: Safe and food-grade additives and colorants are crucial to achieving the desired finish and color of melamine dinnerwares. Ensuring that these additives comply with international safety standards, such as FDA or LFGB, is a vital step in maintaining product safety.
2. Molding and Shaping
Compression Molding: Once the raw materials are prepared, they undergo a compression molding process. Melamine powder is placed into molds and subjected to high pressure and temperature. This process helps shape the dinnerware into plates, bowls, cups, and other desired forms. Precision in molding is essential to avoid defects such as uneven surfaces, cracks, or air bubbles.
Tooling Maintenance: The molds and tools used in shaping melamine dinnerwares must be regularly maintained and cleaned to prevent defects. Worn or damaged molds can lead to inconsistencies in product size and shape, compromising quality.
3. Heat and Curing Process
High-Temperature Curing: After molding, the products are cured at high temperatures to harden the material and achieve its final strength. The curing process must be carefully controlled to ensure that the melamine resin fully polymerizes, resulting in a durable, heat-resistant product that can withstand daily use.
Consistency in Temperature and Timing: Manufacturers need to maintain precise control over the curing temperature and duration. Any variation can affect the structural integrity of the dinnerware, potentially leading to warping or brittleness.
4. Surface Finishing and Decoration
Polishing and Smoothing: After curing, the products are polished to achieve a smooth, shiny surface. This step is essential for both aesthetics and hygiene, as rough surfaces can trap food particles and make cleaning difficult.
Decal Application and Printing: For decorated melamine dinnerwares, manufacturers may apply decals or use printing techniques to add patterns or branding. These designs must be applied carefully to ensure uniformity and adhesion, and they must be tested for resistance to washing and heat exposure.
5. Quality Control and Inspection
In-Process Inspection: Manufacturers should implement quality checks at each stage of production, from raw material inspection to the final packaging. This includes visual inspections, measurements, and functional tests to ensure products meet specifications.
Third-Party Testing: Independent, third-party testing for food safety, durability, and compliance with international standards (such as FDA, EU, or LFGB) adds an additional layer of assurance for B2B buyers. These tests check for chemicals like formaldehyde, which can be harmful if improperly controlled during production.
6. Final Product Testing
Drop and Stress Testing: Manufacturers should perform durability tests, such as drop tests and stress testing, to ensure the melamine dinnerwares can withstand the rigors of everyday use without chipping or breaking.
Temperature and Stain Resistance Testing: Testing for resistance to heat, cold, and staining is essential, especially for products meant for commercial food service environments. These tests ensure that the dinnerware will not degrade under extreme conditions.
7. Packaging and Shipment
Protective Packaging: Proper packaging is critical to prevent damage during transit. Manufacturers must use shock-absorbent materials and secure packing methods to ensure that products arrive in perfect condition.
Compliance with Shipping Standards: Ensuring that the packaging meets international shipping standards helps prevent customs delays and ensures safe and timely delivery to the buyer.
8. Continuous Improvement and Certifications
ISO Certification and Lean Manufacturing: Many leading manufacturers adopt continuous improvement methodologies like lean manufacturing and seek ISO certification. These practices help improve efficiency, reduce waste, and ensure consistent product quality.
Supplier Audits: B2B buyers should prioritize manufacturers who conduct regular audits of their own processes and suppliers. These audits help ensure that the entire supply chain adheres to strict quality standards, reducing the risk of defects or non-compliance.



About Us

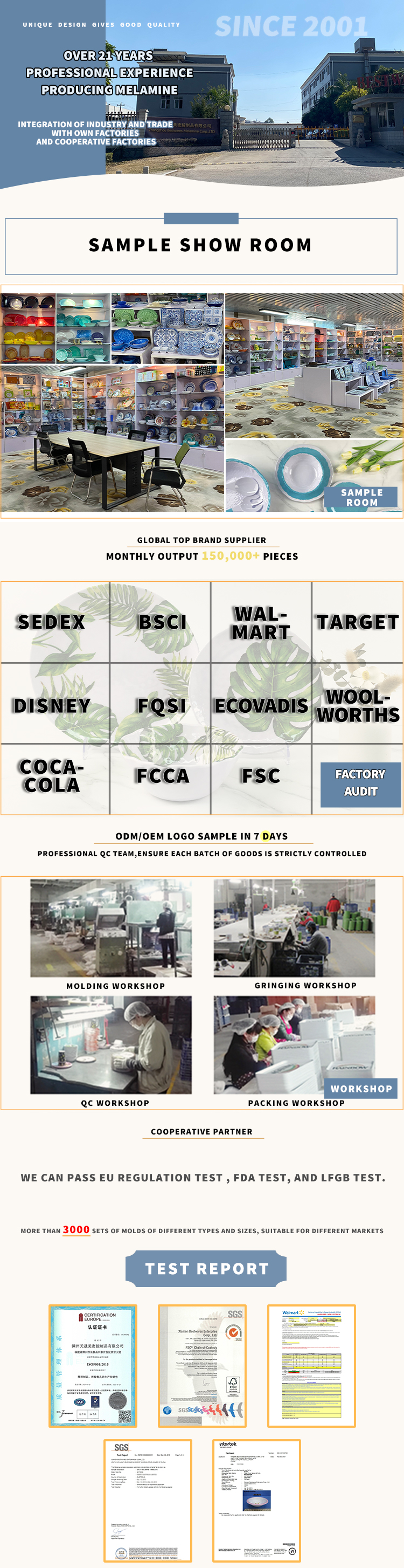
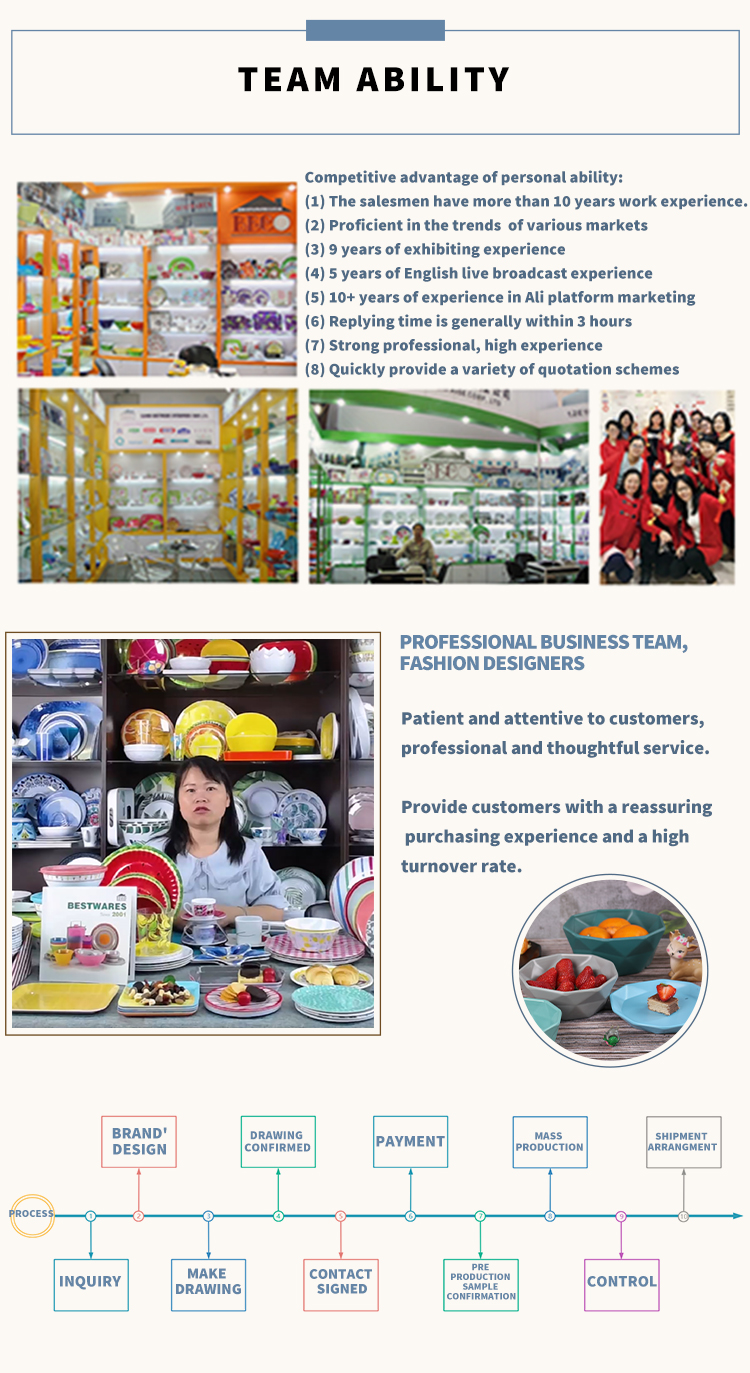
Post time: Aug-23-2024